TPS Fully Digital Multifunctional Welding MachineIn recent years, information technology has developed rapidly, and digital technology has penetrated into all aspects of human society, including welding. In the field of welding, Austrian Fronius launched the world's first fully digital welding machine in 1998, triggering a revolution in the history of welding. Since then, other major manufacturers have followed suit, making digital technology the mainstream in the field of welding. In this wave of revolution, Fronius has always stood at the forefront of the times and led the development of welding technology.Based on the inverter power supply, the fully digital welding machine combines computer technology with a digital signal processor (DSP). The precise calculation of the microprocessor is used to control the various performance and working process of the welding machine. The control circuit is highly integrated and simplified, and the control is unprecedentedly accurate and reliable, with excellent welding performance and perfect welding quality. From MMA to fully automatic welding, it covers the entire range, including welding guns, hoses, cooling devices, welding data files, and even communication interfaces. High-performance processes are used.Fronius's fully digital welding machine adopts a modular design. The welding machine is like a computer, which can be plug-and-play and the software upgrade of the welding machine can be realized to meet various needs and occasions.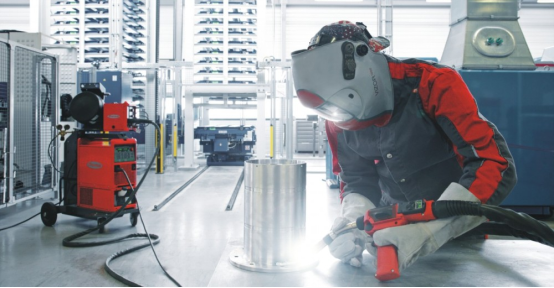
Product Advantages
Accurate arc starting and arc ending
After welding, traditional MIG/MAG welders will have such defects: a ball will be formed at the end of the welding wire, which will affect the re-ignition of the arc. Due to Fronius's superb digital technology, the TPS series welders generate a ball-cutting pulse at the final stage of arc ending. It has the function of droplet separation, which can cut off the ball at the end of the welding wire, thereby ensuring 100% re-ignition characteristics.
(1) Traditional power source: The wire end will form a ball at the end of welding.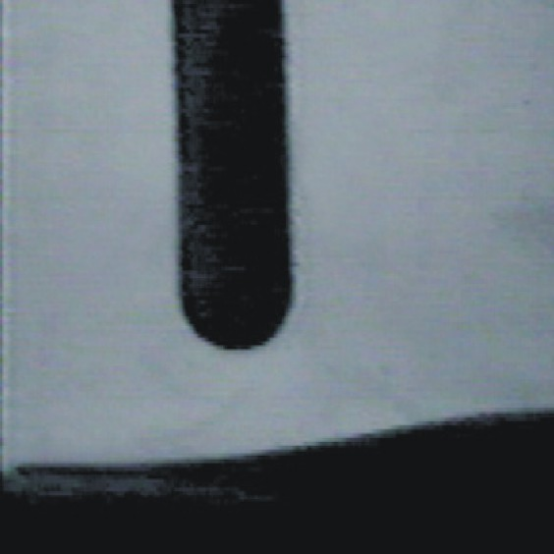
(2) Digital power supply: No balls at the end of the welding wire at the end of welding.
Spatter-free arc starting
Fronius's fully digital welding machine can achieve spatter-free arc starting. At the beginning, the welding wire is slowly fed to the workpiece, stops at the moment of contact, and then a small current is used to start the arc. The welding wire is retracted and when the set arc length is reached, the wire is fed at the set wire feeding speed.
Spatter-free arc starting process:
Wire feeding
When contact is made, wire feeding stops
Wire retraction, arc ignition
The welding wire is retracted to the set arc length
Feed wire forward and start welding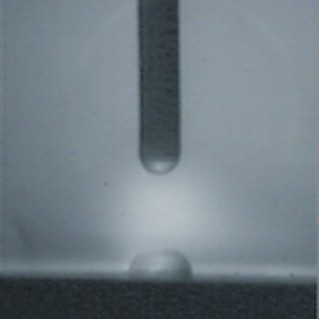
Droplet transfer
Arc control
The TPS series fully digital welding machine controls the arc in all directions. Due to the use of digital technology, the feedback time of the control system is reduced by several orders of magnitude compared to traditional welding machines, greatly improving the sensitivity and accuracy of the feedback.
Safety
The TPS series fully digital welding machine has enhanced its safety function. A special current protection device is installed in the welding machine. When a fault occurs, the protection device will immediately cut off the power supply to prevent the current from passing through the grounding wire and thus destroying the PE system. Secondly, the welding machine is equipped with a constant temperature fan to reduce the accumulation of dust in the machine. At the same time, the welding machine has passed a series of safety tests and has a protection level of IP 23, which is suitable for on-site use.
Application areas
• Machinery repair and maintenance
• Shipyards and construction sites
• Workshops and factories
• Pipeline construction