Industrial robots are becoming a trend because independent and responsive systems can increase productivity and reduce the company's unit cost. The welding operation is improved economically by connecting an automation device to a separate Ethercat CAD robot.ARC, a specialist in welding and cutting equipment in Houston, Texas, USA, produces up to 90% of its products for the oil and gas industry and has customers all over the world. The automated welding and cutting equipment produced by ARC uses standard CAD technology that is widely used in the market, which ensures long-term use. In contrast, when choosing the control device of the equipment, ARC, in order to compete, mostly uses disconnect control systems. The reason is that the control system is a unique design and rarely causes problems in the subsequent maintenance and repair phase. ARC is convinced of this.Automation for fast plasma weldingFor a long time, countless users of ARC have been using the company's plasma welding devices. Plasma welding is very economical compared to laser welding, but the disadvantage is that laser welding alone cannot meet the requirements in the short welding cycle time. The reason is that, although the welding quality of conventional plasma welding devices is high, the plasma welding operation is very slow compared to the laser welding device, and a higher heat input is required during the operation.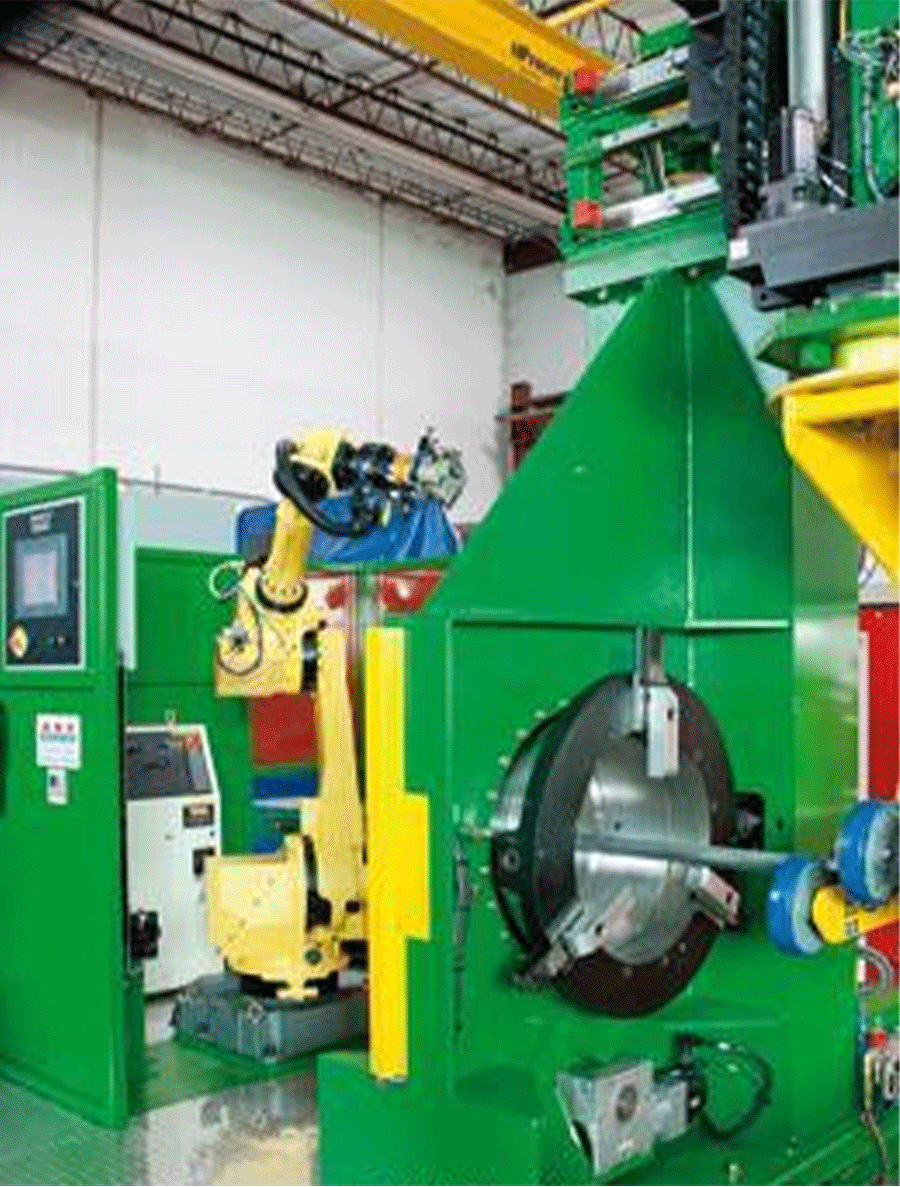
Figure 1 ARC-11-RB welding robot is an automated welding robot for assembly and liquid cleaning equipment
In order to improve the efficiency of plasma welding, ARC has developed a new welding method in its own laboratory, namely triple pulse welding. This new welding method is developed on the basis of the well-known tungsten inert gas welding method. The basic idea of triple pulse welding is based on the use of three different current intensities to achieve a higher heat transfer rate under the condition of weak heat energy. This method can make the plasma welding device achieve similar welding efficiency as the laser welding device, while being very economical.At the request of a large user in Texas, ARC has developed the ARC-11 RB automated welding robot for the installation of liquid cleaning equipment (Figure 1). For this purpose, the triple pulse welding method welding device has been integrated for the first time. The ARC-11 RB automated welding robot is equipped with a Beckhoff CX1010 embedded PC and Twincat NC PTP control device (Figure 2), and its software system uses Windows XP. The compact embedded PC is arranged in a box and is used to control the entire welding device, including the gantry crane in the workshop, the robot function, the operating work surface, the induction heating component, the welding workpiece transport device, and all the components that use compressed air.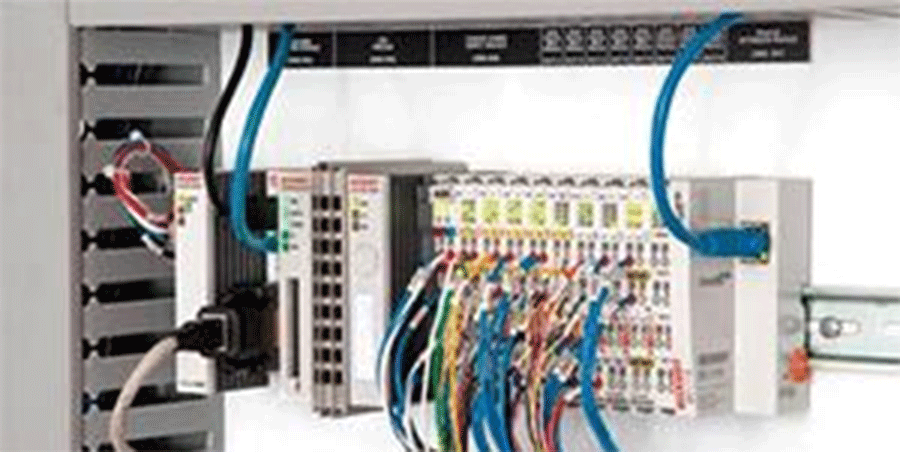
Figure 2 Beckhoff's CX1010 embedded PC with Twincat NC PTP software controls the entire welding process of ARC-11-RB
Due to the use of the above technology, the entire welding process is accelerated and the automation of each step of the entire welding operation is realized. The steps of the entire welding operation are: the gantry crane in the workshop lifts the pipe cut to the rated length and feeds it into a tensioning device (Figure 3). At the same time, the welding robot grabs a terminal ring from the conveyor belt and puts it into the second set of tie rods for positioning (Figure 4). The robot changes the workpiece gripping device to the welding torch and welds the terminal ring to the tube (Figure 5 and Figure 6). After that, the two tensioners are automatically opened and the gantry crane removes the welded workpiece at one end. The tube is then rotated 180°, the other end of the tube is placed in the tensioning device, and the welding process is repeated. When the other end of the welded workpiece is welded, the gantry crane transports the welded tube to a storage rack. Depending on the size of the workpiece, this welding operation lasts up to 2 minutes.The Fanuc Arcmate M 710i C-50 robot is controlled by a Beckhoff CX1010 embedded PC (Figure 7). The Lincoln welding current power supply unit Powerwave R350 is used, which is seamlessly connected directly to the Beckhoff embedded PC via the Devicenet main integrated circuit component. Ethercat terminal blocks serve as the I/O system, and these terminal blocks are arranged directly in sequence on the CX1010 Beckhoff embedded PC. ARC welding devices use the EL403x analog Ethercat output terminal block when the welding operation does not require power supply via the Devicenet interface or when the power supply response time of the Devicenet interface is extremely short during welding.
Welding robot device functions are implemented on the PC-CPUAccording to the requirements of industrial control, ARC has designed its own visualization software for the control interface of the welding robot. By using this software, the welding operator will see the window that he is already accustomed to, just like the original Windows-PC window, which makes it easier and more comfortable to operate the welding robot. Twincat ADS connects the control interface to the control device. Twincat dynamic image converter integrates the welding robot control into the Twincat automation group.Twincat dynamic image converter is transparently integrated into the existing conveyor control range: the robot technology and conveyor control functions are optimized synchronously with Twincat NC PTP (axis point-to-point positioning) or NC I (axis positioning inserted in the three-dimensional image). All NC functions, such as "curve wheel" or "flying saw" (synchronization of the driven axis with the moving main axis), can be connected arbitrarily on a common hardware and software platform. This software and hardware platform also supports various parallel and serial animations: 2D parallel animation, 3D-Delta, splicing animation, Scara, coordinate gantry crane and rotating animation.The programming uses the rules of the coordinate system, where the control calculates the inverse animation of the various related motor positions, the selection and animation configuration are generated in the Twincat system. In the animation channel, for example, the rod length and offset in the Delta type are displayed as data. For dynamic precontrol, the weight and inertia of the welding workpiece can be given in advance. In order to enable the robot to smoothly pick up and put down the welding workpiece, the user can use the "flying saw" and "curve wheel" functions to synchronize them on the conveyor. For the AX 5000 series Beckhoff drives, the Twincat animation converter is optimized (Figure 8).
Here, SPS, motion control, HMI and robotics can only run on industrial PC-CPU. This has the following advantages for users:● No need to set up a separate CPU to control the robot;● Energy costs are reduced because configuration, dataization and diagnosis are carried out in one system;● Twincat is a well-known, integrated configuration, dataization and diagnostic tool;● Losses caused by mismatches are eliminated by the mutual cooperation of various CPUs for SPS, motion control and robotics;● The efficiency and precision of welding operations are improved by adopting a direct interface, which eliminates the tedious mutual cooperation between various CPUs.Automated tensioning of welding workpieces increases production by 30%As mentioned above, during welding operations, the monitoring of welding operations can be achieved through the tracking and inspection function of Ethercat based on all the data of ARC-11 RB. In addition, since all the codes come from the same center, user-specific codes can be parameterized. By using Ethercat, user-specific codes can be written more simply. Because most of the commissions received by ARC are special workpiece welding, the welding robot design commissions accepted by the company are often more troublesome and complicated.If we compare the complexity of the control design of the ARC-11-RB welding robot, it took only 4 weeks from design to application, and the subsequent structure and assembly were completed within 3 weeks. Here, ARC has realized the automated tensioning and removal of the welding workpiece, which has increased the output by 30% compared with the manual tensioning and removal of the welding operation. In this case, only the loading and unloading of the welding workpiece is done manually. Due to the use of Twincat, the axis wiring of the robot control device is based on a simple topology and can be completed in just 1 hour. The control device of the welding robot has few components and a compact structure, so the external dimensions of the distribution box are small.PC control device using Windows software can provide remote controlThe PC control device of the welding robot provided by ARC uses Windows software, so it has the possibility of providing users with remote control. Users can connect to their local area network to realize remote control of the welding robot and can also get online after-sales service from ARC. Welding robot users around the world can get support from ARC in problem analysis through remote control, so as to find the cause of the problems of robot welding equipment and eliminate these problems by changing the software, which greatly reduces the cost of users in the maintenance of welding robot equipment.ARC and Beckhoff have the potential for further cooperation in the Twincat 3 system: the cooperation between the two companies has advantages in forming a unique necessary software environment in terms of integrated machine programming, visualization technology, and HMI visualization. ARC said that in view of the results achieved so far in the cooperation between the two parties in improving the production efficiency of welding operations and reducing production costs, ARC will also use the automation control devices of Beckhoff in Germany on other machines and robots in the future.