Industrial robots are becoming an important force in modern production. Their high precision and large load capacity make them play an irreplaceable role in automated production. However, the accuracy and load capacity of industrial robots do not come from a vacuum. They are affected by multiple core factors. This article will conduct an in-depth exploration of the accuracy and load of industrial robots and reveal the key factors behind them.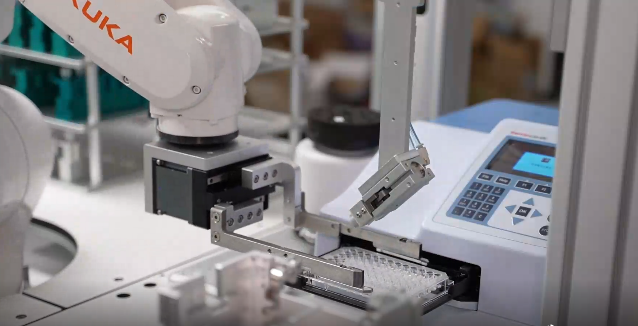
First of all, the accuracy of industrial robots is affected by the mechanical structure. The mechanical structure of the robot includes multiple components such as joints, sensors, and drivers. The accuracy and stiffness of the joints determine the movement accuracy of the robot, while the accuracy of the sensor directly affects the robot's perception ability. The accuracy and response speed of the driver also have an important impact on the position control of the robot. Therefore, optimizing the design of mechanical structures and selecting high-precision components can improve the accuracy of industrial robots.
Secondly, the load capacity of industrial robots is closely related to the power system. The power system includes motors, reducers and transmission systems, etc. Their performance will directly affect the load capacity of the robot. The power and torque of the motor determine the carrying capacity of the robot, while the transmission efficiency of the reducer affects the working stability of the robot. Therefore, when selecting a power system, it is necessary to comprehensively consider the load requirements of the robot and select appropriate motors and reducers to ensure its stable and reliable operation.
In addition, the control system is also one of the important factors affecting the accuracy and load of industrial robots. The control system includes components such as controllers and encoders, which are responsible for precise position and force control of the robot. The accuracy and response speed of the controller determine the movement accuracy of the robot, while the accuracy of the encoder directly affects the position detection and closed-loop control of the robot. Therefore, optimizing the design of the control system and selecting high-precision controllers and encoders can improve the accuracy and control performance of industrial robots.
In addition, the working environment and usage conditions of industrial robots will also affect their accuracy and load capacity. For example, in a high-temperature environment, the robot's sensors and controllers will be affected by temperature and produce errors, which will affect the accuracy of the robot. In harsh working environments, such as dust, vibration and other conditions, the robot's components are easily damaged, thereby reducing its load capacity. Therefore, when designing and using industrial robots, it is necessary to fully consider the impact of the working environment and take corresponding measures to ensure its working stability and performance.
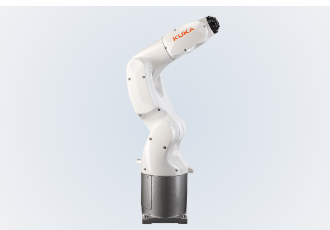
To sum up, the accuracy and load capacity of industrial robots are comprehensively affected by multiple factors, including mechanical structure, power system, control system, and working environment. Optimizing the design of these key factors and selecting appropriate components can improve the accuracy and load capacity of industrial robots, thereby achieving more efficient and stable automated production. Industrial robots will continue to develop and innovate, becoming important assistants in modern production and promoting further progress in the industrial field.